GAMP 5: Concept of GAMP 5 in Pharmaceuticals
GAMP-5 Good Automated Manufacturing Practice consists of guidelines aimed at both users and manufacturers of automated pharmaceutical products. Established in 1991 by professionals in the UK pharmaceutical industry, GAMP seeks to address the industry’s needs and enhance compliance with evolving European regulatory expectations. Its primary focus is to provide clarity on how pharmaceutical companies should validate their computer systems.
GAMP-5, the fifth edition of the GAMP guidelines, was published in February 2008 by the International Society for Pharmaceutical Engineering (ISPE), a collaborating organization with GAMP.
GAMP seeks to provide an economical framework of best practices to ensure that computerized systems are efficient, high-quality, suitable for their intended purposes, and compliant with relevant regulations.
The second edition of ISPE GAMP® 5: A Risk-Based Approach to Compliant GxP Computerized Systems maintains the core principles and framework of the original edition while updating their relevance in today’s landscape. This includes acknowledging the growing significance of service providers, adapting to evolving software development methodologies, and embracing the expanded utilization of software tools and automation. It emphasizes the necessity of informed decision-making by skilled subject matter experts in determining appropriate strategies.
The ISPE GAMP 5 Community of Practice (CoP) continually evaluates and revises GAMP practices in light of current industry standards, regulatory requirements, and technological advancements. The second edition of ISPE GAMP 5 reflects:
- The heightened importance of service providers, encouraging regulated entities to maximize collaboration with suppliers to capitalize on their expertise, knowledge, and documentation.
- The evolving nature of software development practices, stressing that the GAMP approach to specification and verification accommodates iterative and incremental methodologies alongside traditional linear processes.
- The increased adoption of software tools and automation to enhance control, improve quality, and mitigate risks throughout the lifecycle of computerized systems.
Moreover, the guide underscores the critical role of “critical thinking” by experienced subject matter experts in tailoring approaches to specific circumstances.
This version is considered the most organized and project-based method, emphasizing risk control and quality management in the computerized systems used for manufacturing and supplying pharmaceutical products.
The advantages for pharmaceutical companies implementing GAMP 5 guidelines lie in their ability to ensure the desired standards of product quality. While GAMP 5 isn’t regulatory in nature, it offers a framework of principles and procedures aimed at guaranteeing the quality standards of manufactured pharmaceuticals. Many pharmaceutical companies striving for automated systems suitable for their intended purposes have embraced these guidelines. GAMP 5’s practical guidance is centered on four core principles.
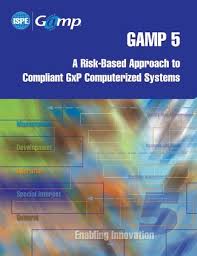
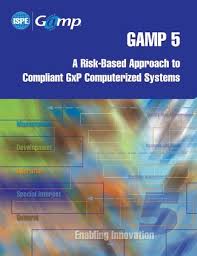
This procedure serves multiple purposes in aiding users in understanding regulatory requirements for manufacturing computerized pharmaceutical products. It not only establishes a shared language and terminology to ensure a structured and clear approach to production but also advocates for a systematic life cycle approach encompassing all stages from raw materials to finished products in accordance with best practices. Additionally, it delineates the roles and responsibilities of each participant along the production line, including suppliers, fostering collaboration and coordination between stakeholders. By providing a comprehensive framework for users and suppliers to operate within, this guideline emphasizes the importance of cooperative engagement throughout the production process.
The GAMP guideline outlines principles to ensure that automated systems are suitable for their intended use prior to the production of pharmaceutical products. It guides suppliers in identifying and addressing any potential defects in the system, thereby ensuring that the products supplied by the pharmaceutical industry meet stringent quality standards. GAMP follows a risk-based approach to compliance.
Despite its numerous benefits, implementing GAMP presents challenges, with the primary hurdle being the establishment of procedural control. While GAMP offers guidelines for validating automated systems according to standards, it lacks a procedure for verifying the effectiveness of existing processes.
GAMP 5, or Good Automated Manufacturing Practice, is a set of guidelines for manufacturers and users of automated systems in the pharmaceutical industry. Released by the International Society for Pharmaceutical Engineering (ISPE), GAMP 5 aims to ensure that automated systems are fit for their intended use and comply with regulatory requirements.
Key Aspects of GAMP 5
- Risk-Based Approach: GAMP 5 emphasizes a risk-based approach to compliance, focusing on identifying and mitigating risks that could affect product quality or patient safety. This approach allows for more efficient use of resources by prioritizing efforts on critical aspects of the system.
- Life Cycle Management: It promotes a life cycle approach to system management, from initial concept through to retirement. This includes stages such as planning, specification, design, testing, and maintenance, ensuring that the system remains compliant and fit for purpose throughout its operational life.
- Scalability: The guidelines are scalable, meaning they can be applied to both simple and complex systems. This flexibility allows organizations of various sizes and complexities to implement GAMP 5 principles effectively.
- Supplier and Service Provider Collaboration: GAMP 5 encourages collaboration with suppliers and service providers to ensure that all parties understand the requirements and work towards achieving compliant systems.
- Documentation: Proper documentation is critical in GAMP 5. This includes clear and concise records of system requirements, design, testing, and maintenance activities. Documentation helps in demonstrating compliance and provides a basis for continuous improvement.
- Quality Management: Integrating GAMP 5 principles into the overall quality management system ensures that automated systems are considered within the broader context of product quality and regulatory compliance.
Implementation in the Pharmaceutical Industry GAMP 5
Implementing GAMP 5 in the pharmaceutical industry involves adopting its principles throughout the entire system life cycle. Companies must conduct risk assessments to identify critical aspects that impact product quality and patient safety. Documentation and collaboration with suppliers are essential for maintaining compliance. Regular reviews and updates to the system ensure it remains effective and compliant with current regulations.
By GAMP 5 guidelines, pharmaceutical companies can improve their automated systems’ efficiency, compliance, and reliability, ultimately ensuring high-quality products and patient safety.